1. 胺液吸收/再生工艺概述
要想满足最终产品销售规格要求以及符合环境排放限值,从工艺流和天然气中除去硫化氢(H2S)和二氧化碳(CO2)为必要的质量控制措施。
这些酸性污染物一般采用可再生工艺从一烷醇胺和/或烷基烷醇胺的水混合物中除去。酸性工艺蒸汽和富胺(是指含有大量硫化氢和二氧化碳的胺)溶液的处理通常会因这些化合物的性质导致腐蚀。腐蚀过程以及泄漏和故障隐患的加速可能会导致计划外停产,最终对工厂收入造成严重影响。
利用多级吸收塔中的稀胺水溶液,在进气压力下,采用逆流反应吸收方式从气流或液体工艺流中去除酸性气体。碳氢化合物及其他非反应溶解气体通过降低闪蒸罐中压力,从胺水溶液中收集。根据胺溶液化学特性,在高温下,通过逆流气提法,从浓胺溶液中去除酸性气体。这就是胺再生步骤。用来加热和酸性气体稀释的汽提蒸汽在低压下操作多工位再生器与浓胺接触。再沸器通过汽提部分下方再生器塔底部给料,从而减少水用量。酸性气体与塔顶回流槽中的冷凝水分离。浓胺/稀胺换热器将胺再生塔能耗降到最低。再循环返回到吸收塔顶部之前,通过浓/稀胺换热器、稀胺冷却器及过滤系统从再生器底部抽取热/稀溶液。
2. 胺液装置内部腐蚀问题概览
液胺系统受蒸汽相、胺溶液中、再生器回流中二氧化碳和硫化氢以及胺溶液中胺降解产物腐蚀威胁。在各个炼油厂中,液胺系统也面临天然气和合成气中一般没有发现的几种元素的腐蚀威胁,如氨气、氢氰酸以及有机酸,这些元素将在炼油厂液胺系统周边各点聚集。
评估胺液装置腐蚀隐患需要使用几个关键变量,因此如果没有在线监测,腐蚀预测将变得非常复杂:
• 酸性气体加载;
• 速度和壁剪应力;
• 温度;
• 杂质及热稳定胺盐;
• 二氧化碳-硫化氢比;
• 胺液类型选择
图1:展现出高风险腐蚀区域的胺液装置工艺流程图
上文中图1显示为给定氨酸气体装载和速度时碳钢腐蚀率预计变化。
图2中简化工艺流程图展示了极有可能造成腐蚀和结垢的各个区域示意图:
图2:展现出高风险腐蚀区域的胺液装置工艺流程图
如图中所示,胺液设备中腐蚀可以分为两种类型:
• 二氧化碳和硫化氢通过一层薄液膜与铁反应造成的碳钢湿酸性气体腐蚀;
• 出现胺液时造成的碳钢胺液腐蚀。
非隔热胺吸收塔会出现水蒸汽冷凝。由于与二氧化碳一同出现的硫化氢非常少,因此可能形成碳酸,最终导致碳钢腐蚀加速,尤其是吸收塔底部的蒸汽空间。
工艺流中的沉淀物(比如铁基腐蚀产物)可侵蚀出口喷嘴,并在闪蒸罐中聚集,最终导致垢下腐蚀风险增加。
稀/浓胺换热器中,由于浓胺流背压不足,导致水溶液沸腾和/或酸性气体汽提出现两相胺流。在板框式及和管壳式稀/浓胺换热器中出现快速金属表面变薄和过度振动。逆流设计最大程度地回收热量,但是也造成了腐蚀后果。为了防止结垢,通过管侧加入浓胺溶液时,与如果将稀胺溶液布置在管侧时相比,在壳顶部形成泡泡的可能比较大。不可冷凝的气体,比如空气和碳氢化合物,会在壳中聚集,阻止胺溶液打湿金属表面。在酸性气体只有二氧化碳或者再生胺溶液含量非常低时,尚未被胺溶液打湿的碳钢表面在水蒸汽冷凝区域容易遭受碳酸腐蚀。
再生器入口另外一个常见问题是两相进料模式,这可能造成进料点对面容器壁的腐蚀以及造成蒸汽小液滴传输偏离再生器。
再沸器进给压力是促使两相流在再沸器适当工位的重要设计参数。不对称流动条件以及流动障碍(比如传统侵入腐蚀监测)已被证实会造成高速蒸汽流扰动上升,加快下流金属表面的腐蚀。
绝对流速、扰动以及蒸汽速率也是塔顶冷器和收集器部分中发生的腐蚀和侵蚀控制关键。冲向下游金属表面的蒸汽可能会造成设备壁腐蚀,硫化铁钝化层可轻易地被去除,使表面裸露被进一步腐蚀。
胺处理装置中热稳定性盐也存在腐蚀隐患。热稳定盐是胺与强酸性化合物(如二氧化碳)反应后产生的反应产物。这些产物通常同补充水和进气流引入,或者在装置内同其他污染物(比如氧气、一氧化碳、氰化物和二氧化硫)发生化学反应生成。按照再生塔中使用的工艺条件,热稳定性盐不可再生,因此这些盐聚集在整个工厂的胺中,从而造成严重腐蚀。腐蚀产物本身,硫化铁以及碳酸铁以固体微粒形式在循环胺中产生,能够造成其他经营困难,比如泡沫、污垢和乳液。这在经营、产量、处理能力以及吸收能力方面会影响液胺装置稳定性。
3. 胺液装置关闭的商业影响
像酸性水汽提装置那样,胺液装置是炼油厂遗忘的“老黄牛”之一——大多数情况下,当胺液吸收和再生系统能够按照要求运行时,炼油厂经营者和工程师不需要太多注意和关注。但是,除非准备足够的胺液处理冗余能力,胺液系统故障可能会成为经营活动的一个主要问题——最后,在执行修理时,这可能会造成工厂全面停产。
许多情况下,原工厂建设期间,资本成本会对产量扩展项目,尤其是炼油清洁燃料项目形成制约,最终造成大多数工厂胺设施缺少备用生产能力或冗余。有些工厂采用多条平衡的液胺再生输送系统以确保液胺系统各个部分能够关闭进行一段时间的维护保养——但情况并非都如此——尤其是那些空间和重量极其有限的近海生产设施。炼油行业中,由成品石油、航空燃油及柴油更低硫含量规格要求促使氢化处理装置的运营难度不断上升,从而增加了胺吸收和再生系统的压力,最终硫化氢量会增加。某些情况下,原来设施是在更高加工率的情况下工作的,硫化氢装载量超过原设计量,这成为从不断上升的项目预算中保留资本的一种手段。
反过来,这限制了炼油厂的灵活性,如果因胺液中释放出来的硫化氢气体导致风险,不能存放大量胺液,那么炼油厂将不得不关闭胺液系统进行修理。
如果不能存放大量胺液,那么炼油厂将被迫通过下列方式限制胺液系统上的硫化氢载荷:
• 改变进料(将重型高硫原油改变为轻型低硫和更加昂贵的进料);
• 降低生产率(降低进入天然气加工平台或岸上工厂的天然气进料率);
• 改变生产模式(向仓库输送高硫原气油进行后续加工,而不是输送超低硫高价值柴油)。
胺液系统停产期间,如果硫化氢产量比较低,也会对下游硫回收装置的经营活动造成困难,出现气流量大范围变化不稳定的现象,最终导致反应釜管道或液硫储罐的浸如管被堵塞。
没有充足胺液能力的持续运营将可能导致破坏设施气体排放质量限值,从而导致地方和/或国家监管机构对工厂经营发布执法命令和/或施加更加严格的监管。
胺液系统停产对特定工厂造成的商业影响将取决于工厂类型,工厂特定配置以及进料质量,但是通常都是很严重的。
在炼油厂内,假设胺液装置停止工作5天进行修理导致炼油厂产量平均减少10%,炼油毛利润率为7美元/桶,日产量200,000桶的炼油厂的商业影响将达到70万美元,另外还有修理成本,比如对存在高腐蚀风险的胺液装置浓/稀胺换热器管板更换需要30万美元。因此,预计胺液再生输送系统计划之外停止工作5天将导致炼油厂(即使备有冗余生产能力)100万美元以上的生产损失。
对于一家5亿标准立方英尺/日生产能力的大型天然气加工厂,假使因计划之外的液胺系统停产导致产量下降25%,按照天然气主导销售价格$3/MMBTU(2014年-2016年Henry Hub平均报价)来计算,那么如果停产5天,则该工厂的收入亏损将大约为40万美元,另外加上维修成本,最终所损失的机会价值能轻易地突破60万美元。
4. 永感™传感器建立了胺液装置安全和可靠运行的信心
永感™连续式壁厚测量传感器设计用于各种工业环境,是用来监测胺液装置最高风险区域的理想产品。这些传感器以无线方式与中央网关进行通信,中央网关直接将数据传送到整合或操作工程师办公桌上,从而避免进入装置获取或收集测量数据。
有了监测数据,工程师就能可靠地判断设备高风险区域内是否发生腐蚀,从而帮助他们很好地按计划停机检修,管理好装置完整性。这些数据在理解腐蚀率和进料和工艺条件变化(尤其是因短期不稳定引起的变化)相互关系,将泄漏风险降到最低以及更好地预测设备停机等各个方面极具价值。
永感™系统支持防腐减腐策略优化,同时能够发送相关数据,提供防腐合金冶炼学性能升级决策的理论证据支持。
5. 胺液系统高风险位置永感™ 解决方案
下文图3所示为胺液装置可能用到的永感™腐蚀监测系统示意图:
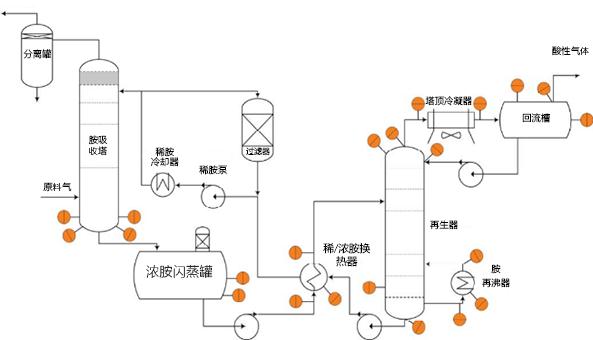
图3:胺液装置监测位置示意图
潜在监测位置如上文图3所示。一般安装会设置大约20个监测位置,每个位置设2-4个传感器。
耐高温——可以提供三种波长,即100毫米、300毫米以及500毫米的各种传感器。对于胺液系统内大部分位置,能够抵抗150?C (300?F)高温的100米波长传感器比较合适。靠近再生塔重沸器等较高温度位置,一般需要使用能够抵抗600?C (1100?F)高温的标准300毫米波长传感器。
图4:放置在夹具总成上的100毫米短波传感器
冶金学要求——传感器可安装在各种材料上,包括碳钢和铸碳钢、铬钢(1% Cr (5130), P5, P9)、双相钢、P265GH (430?161)、1.4571 (316Ti)、 P295GH (17Mn4)、蒙乃尔合金、HR120、因康镍合金、耐热镍铬铁合金和哈氏合金。
传感器安装方法——采用螺钉安装方式可灵活选择监测位置。可将螺钉焊接到工作管道上和危险区域,比如使用摩擦螺钉焊接方式。
图5:采用螺钉安装方式的传感器安装情况
因材料限制不准许或不可能进行焊接时,永感™可提供最大40英寸的各种直径夹具,而对于汽提塔和各种容器,可采用专门定制安装架;这些夹具和安装架能够通过磁性固定在容器上,如果没有使用磁性材料,可用环氧胶进行固定。
图6:传感器安装使用的环氧胶安装架
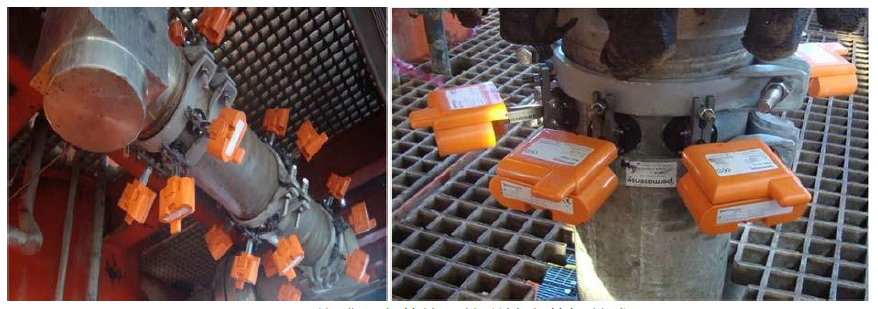
图7:传感器安装使用的夹具总成
6.永感™ ET210型号传感器的介绍
Permasense最近引入了适用于更低温度(120°C (250 °F)) 应用环境的ET210型传感器,这种传感器成为酸性汽提装置大部分区域监测的理想产品。这类传感器采用专门设计的极低功率EMAT技术,这种技术可以通过1毫米厚的外部防腐保护层探测金属厚度,不会造成任何损坏。这种极低功率要求使基于EMAT的技术成为厂家首先选择布置在设备0区本质安全特定区域。通过内置磁体,将每个传感器放置在设备外部;采用遵守WirelessHART协议的通信方式和电池电量,内置磁体让安装变得快捷和方便。采用二级塑料环将传感器固定到位,如图9所示;另外,穿过传感器主体连接钢带,防止传感器掉落。安装传感器之前,需要对测量位置进行表面清理,比如用钢丝刷和光砂纸打磨。因此,只需要几分钟就能安装好每个传感器。
如图9所示,可采用圆周布局方式轻易地安装ET210型传感器,监测局部腐蚀机理。
图8:ET210传感器。安装时不需要侵入,不需要除去漆料,采用轻型固定环进行磁性安装。
图9:ET210传感器圆周布置方式
7.布置举例
案例研究——欧洲炼油厂经营四条平行液胺输送系统——每条系统都采用类似配置,在关键位置使用永感™传感器技术进行实时腐蚀监测。
图10:客户液胺系统管道及仪表流程图摘录
以下趋势图所示为每个输送系统在液胺再生塔上安装的每个传感器从2012年7月到2014年7月的永感™数据,编号为1-4。
虽然很明显在胺输送系统1-3中没有出现或者出现少许腐蚀活动,但是在液胺输送系统4中同样位置,测量发现腐蚀率达到1毫米/年(40密耳/年)。
有了永感™数据,工厂腐蚀工程师就能够清楚地向那些进一步实施调查的操作/技术员工展示四个输送系统的性能差异。我们发现,由于从各个上游装置来的酸性气流排列不一致,输送系统4进气的二氧化碳含量比其他三个输送系统高得多。因此,我们可以改变进气路线,让四个输送系统的高二氧化碳含量酸性气体尽量平均,以限制腐蚀效力。
结论:
1. 永感™数据核实到第4输送系统中本来没有预计或探测到,直到下次停机(如果设备泄漏提前发现,则在设备泄漏之后)才发现的腐蚀问题。
2. 第4输送系统液胺装置寿命可延长多年,从设备推迟废弃和更换成本中为客户节约大量成本净额,同时也避免出现计划之外的停产。
3. 本次案例研究也展示了永感™数据的效力,这些数据与工艺数据一起,为整个工艺技术/操作以及完整性管理/腐蚀/检查功能提供坚实的问题解决基础,同时促进工艺改变,以减轻腐蚀情况。